Sessant’anni di storia, dal boom economico ai giorni nostri, caratterizzati dall’innovazione. E oggi, come tutto il mondo industriale evoluto, è alle prese con la sfida della transizione ecologica. È la storia di Brianza Plastica, che nel lontano 1962 iniziò a produrre rotoli e lastre in vetroresina per i settori commerciale e industriale.
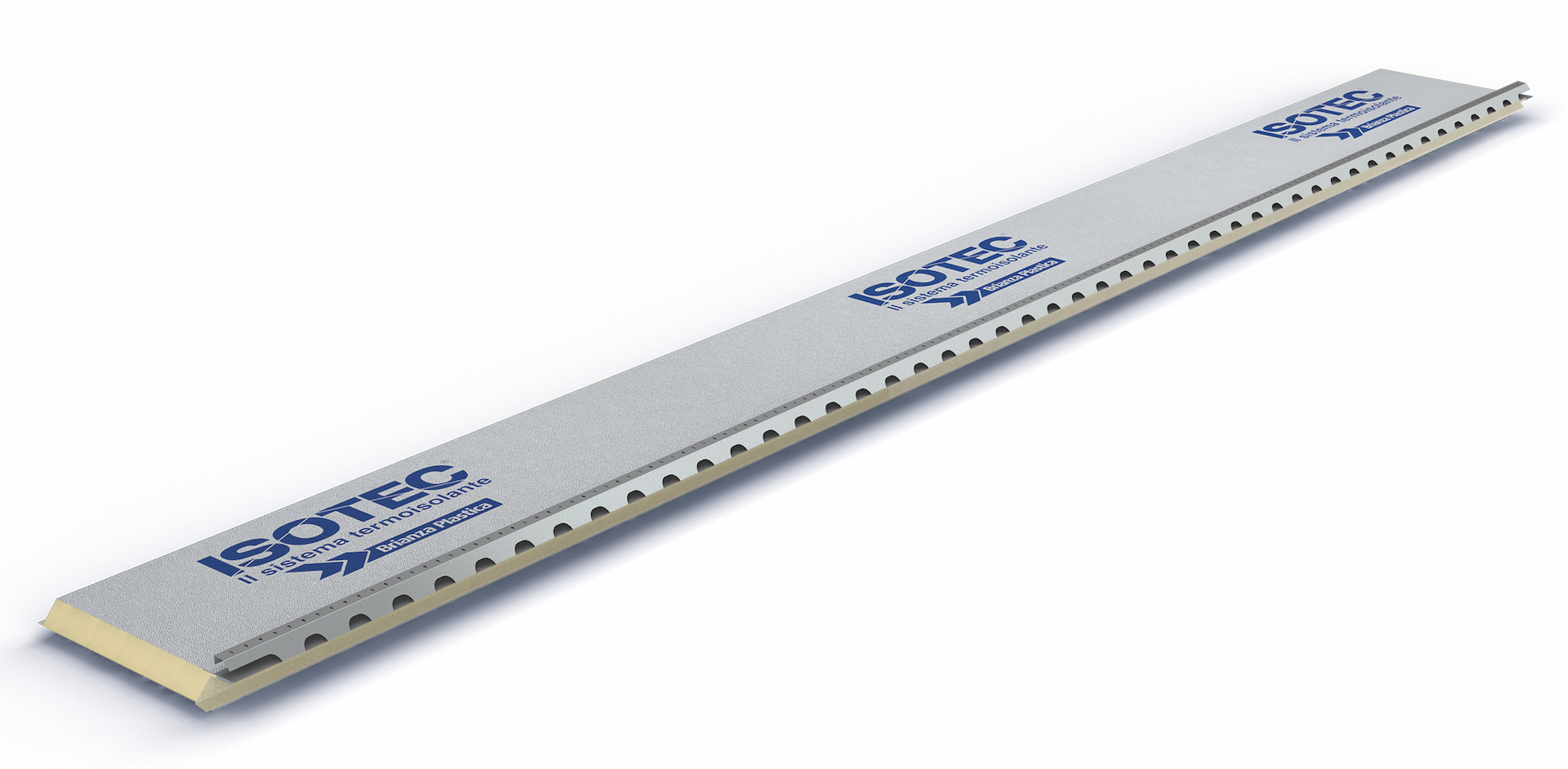
Vent’anni dopo l’azienda di Carate Brianza si affacciò sul mercato dei sistemi per l’isolamento termico per gli edifici residenziali e industriali e nel 1984 nacque Isotec, il pannello termoisolante sottotegola in poliuretano, con correntino integrato.
Oggi, dopo sei decenni esatti dall’avvio e 300 persone alle dipendenze, cinque sono le sedi produttive: oltre a Carate, sono attivi i due siti di San Martino di Venezze in provincia di Rovigo e quelli di Ostellato vicino a Ferrara e di Macchia di Ferrandina, nei pressi di Matera.
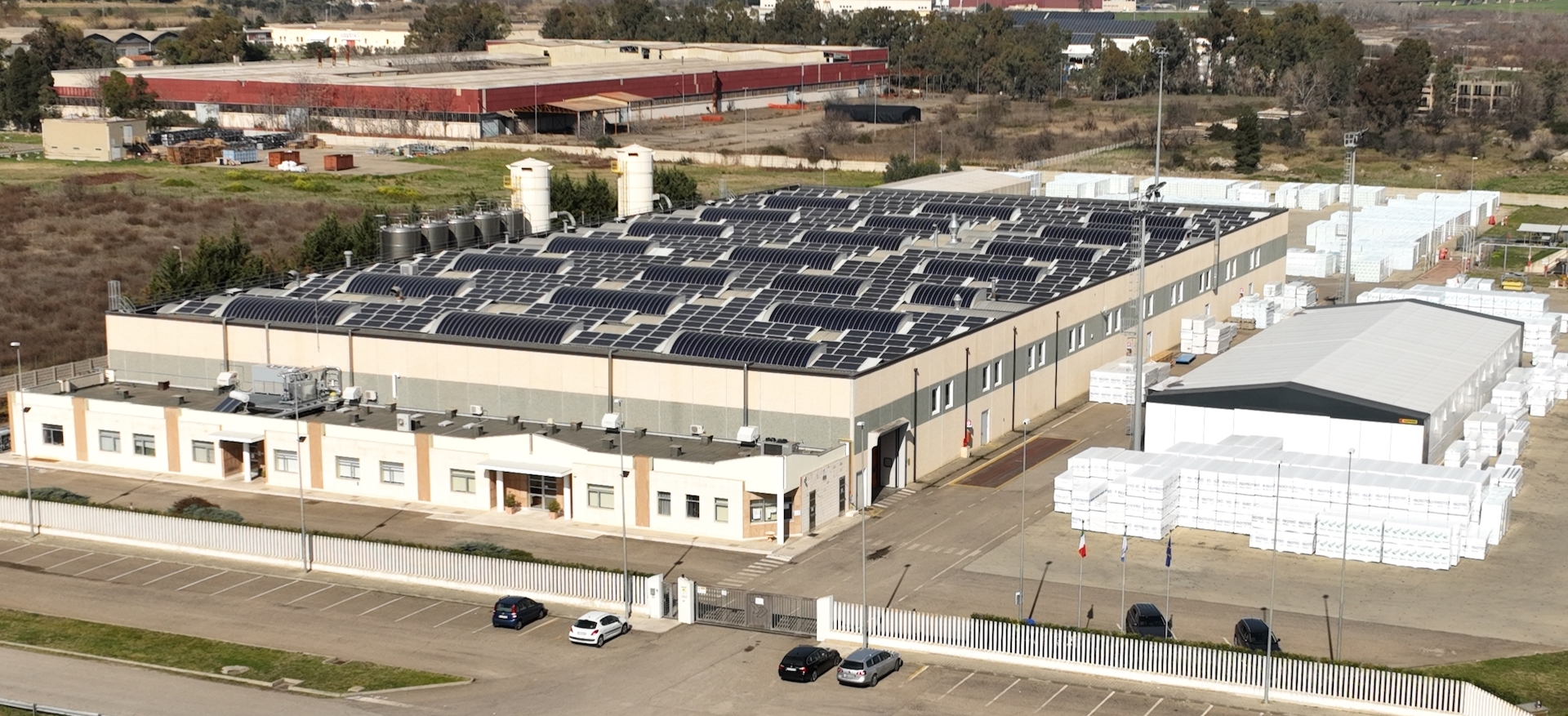
A questi si aggiungono le sedi logistiche di Nola vicino a Napoli, Lione in Francia ed Elkhart negli Stati Uniti. Anni di ricerca e d’innovazione che hanno portato i prodotti delle gamme Isotec, Elyfoam e Xroof a ottenere la conformità ai requisiti Cam e la mappatura Leed V4.
Per un’azienda che, oltre ai prodotti termoplastici, tratta anche quelli termoindurenti, la transizione ecologica è una sfida particolarmente impegnativa, ma è soprattutto vista come opportunità di mercato, non solo dal punto di vista dell’innovazione dell’azienda, ma per l’intera filiera produttiva, con l’obiettivo di offrire al mercato prodotti con quote di riciclato sempre maggiori.
Proprio sul fronte della sostenibilità, due anni fa l’azienda ha avviato una partnership con una società di gestione del ciclo dei rifiuti con lo scopo di nobilitare il fine vita dei propri scarti e dei residui di produzione in vetroresina, materiale che, come si sa, presenta poche soluzioni sostenibili di riciclo.
Grazie a quest’accordo, la quasi totalità degli scarti derivanti dal processo produttivo vengono oggi destinati a cementifici e acciaierie sotto forma di combustibile da rifiuto, che va a ridurre l’utilizzo di combustibili fossili e le emissioni di CO2 in atmosfera.
Un progetto, tra i diversi avviati, che testimonia l’adesione di Brianza Plastica al modello di economia circolare e di sostenibilità anche per il mondo dei laminati in vetroresina.
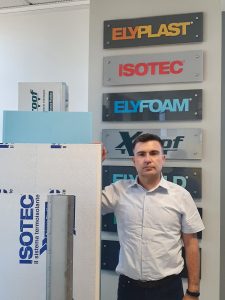
A illustrare il cambio di paradigma è Gabriele Chini, responsabile gestione qualità, sicurezza e ambiente di Brianza Plastica, che ricorda come da alcuni anni la società ha rivoluzionato lo storico sistema di imballaggio dei pannelli della gamma Isotec, iniziando a sostituire, nel sito produttivo principale di Carate, il film termoretraibile con uno nuovo estensibile, più leggero e riciclabile al 100%.
Una scelta che ha portato un risparmio di energia da fonti non rinnovabili pari a 21 Tep all’anno e, soprattutto, un minor consumo di plastica per unità di imballo del 25%. Altro fronte d’impegno ha riguardato il tema dell’ecodesign: a partire dal 2020, nella progettazione e sviluppo dei prodotti, l’azienda adotta le linee guida fissate dalla norma internazionale Iso 14006.
Da Carate ci tengono poi a far conoscere il loro punto di vista circa l’impatto ambientale dei loro prodotti: consapevoli che non si tratti di prodotti di origine naturale, il management sostiene che l’impatto debba essere calcolato sul ciclo di vita utile del prodotto stesso, che per i materiali isolanti viene valutato in 50 anni e che in questo arco di tempo consente di risparmiare molta energia.
In generale, l’approccio dell’azienda alla sostenibilità si concentra su tre fattori: prodotti, con materie a minor impatto ambientale; processi, per ridurre le quantità di rifiuto; siti produttivi, con interventi di revamping delle linee di produzione per l’efficientamento energetico e l’installazione di impianti fotovoltaici in copertura (a Rovigo e a Ferrandina sono già attivi due impianti da fonti rinnovabili).
Infine, i dati ambientali. Con il prossimo anno l’azienda conta di ultimare l’analisi dei fattori legati alla sostenibilità sia ambientale che sociale ed economica, per arrivare l’anno successivo a produrre un rapporto di sostenibilità.